SAFETY MANAGEMENT SYSTEMS
Learn how to implement safety management systems such as ISO 45001 and ANSI/ASSP Z10 that have elevated the landscape of safety with goal setting, planning and measuring performance.
Beyond Compliance: A Healthier Workplace Is a Safer Workplace
Monday, February 12 | Advanced | 0.7 CEUs
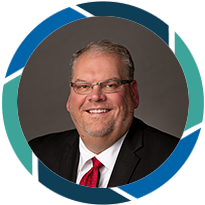
In an evolving landscape, organizations must redefine their approach to safety and health programs, aligning bottom-line objectives with workplace well-being. Safety and health initiatives often exist in isolation within separate organizational divisions, hindering their impact and potential. This course aims to bridge the gap between these programs, fostering integration to maximize results and improve outcomes.
Instructor(s): Todd R. Hohn, CSP
- Analyze key issues workers face due to changing workplace dynamics
- Demonstrate how aligning safety and health strategies can yield measurable benefits
- Review case studies showing how companies have successfully integrated safety and health
- Discuss best practices for promoting a safer and healthier workplace
- Develop strategies to shift management's perception of safety and health
Conforming With ANSI/ASSP Z16.1: Creating a Balanced Set of Metrics
Monday, February 19 | Intermediate | 0.4 CEUs
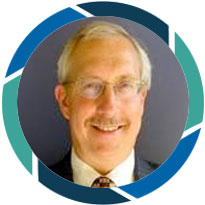
Discuss effective strategies and skills to implement a balanced set of metrics to evaluate your organization's occupational safety and health performance. Through a focus on the leading, lagging and value-based metrics outlined in the ANSI/ASSP Z16.1 standard, you will deepen your understanding of how these metrics can help you drive organizational improvement, elevate risk management and enhance your organization’s overall performance. A copy of the ANSI/ASSP Z16.1-2022 Safety and Health Metrics and Performance Measures is included.
Instructor(s): Paul A Esposito, CSP, CIH
- Apply the principles and concepts of a balanced set of leading, lagging and value-based metrics
- Interpret and analyze value-based metrics that impact an organization's financial results to identify opportunities for improvement
- Demonstrate how your organization can use multiple leading metrics to predict and influence lagging metrics
- Communicate the relationship between a balanced set of metrics and effective risk reduction
- Align safety metrics with organizational goals and performance objectives
Corporate Safety Management
Monday, February 12 – Wednesday, February 14 | Intermediate | 2.1 CEUs
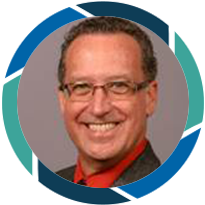
Learn new ways to tackle challenges, craft solutions and apply the skills needed to successfully position safety in your organization. Explore corporate management systems and organizational cultures and develop insight on how you can influence them from a safety perspective. You will review corporate reporting relationships, occupational safety and health (OSH) staffing and the tenets of OSH management systems. You will also use tools to assess your organization’s current safety process and identify ways to adjust it to achieve desired state. Develop your ability to apply negotiation and leadership skills to influence decision-making that affects corporate structure. Take away a new understanding of how to apply corporate safety management concepts and systems and how to lead and influence positive outcomes that change your workplace. This course is the third in a three-course series for obtaining ASSP’s Safety Management Certificate. Your registration includes a copy of ISO 45001-2018.
Instructor(s): James Boretti, CSP
- Develop a safety management system to support your organization’s strategic and business goals
- Effectively assess and measure your organization’s safety performance
- Discuss the influence of corporate culture and develop skills to effect changes that help your organization embrace OSH efforts
- Justify where the safety function is best positioned within your organization’s corporate structure
- Apply leadership, negotiation and communication skills to positively influence corporate safety management system
- Analyze key initiatives for creating high-impact safety performance
- Define and discuss best practices for safety performance enhancement
- Analyze appropriate adjustments to the safety effort in response to corporate mergers, downsizing, rightsizing and reorganizing
Implementing ISO 45001
Monday, February 19 – Wednesday, February 21 | Intermediate | 2.1 CEUs

Through a blended learning approach, develop the knowledge and confidence to successfully implement an occupational health and safety management system (OHSMS) as an integral part of your organization’s overall business operations and objectives. Organizations that adopt the standard as part of their business practices, goals and objectives can better protect their workers, brand reputation, supply chain and future growth on a global level. Your registration includes a digital copy of ISO 45001-2018.
Instructor(s): Victor M. Toy, CSP, CIH
- Create a compelling story around developing and implementing an ISO-45001-compliant OHSMS
- Explain the importance and value of implementing an OHSMS following the ISO 45001 standard
- Define key terminology and guidelines related to the implementation of the ISO 45001 standard
- Navigate the ISO 45001 standard and its main sections
- Assess performance of your OHSMS, leveraging the success factors listed in the standard to continuously improve the process
- Translate knowledge gained into an actionable plan for initiating your own OHSMS development and implementation
Internal OHSMS Auditing Using ISO 45001
Thursday, February 22 – Friday, February 23 | Intermediate | 1.4 CEUs
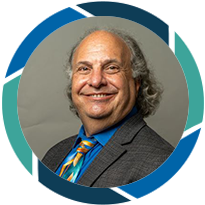
Examine ISO 45001-2018 from an auditor's perspective. Review components of an effective internal audit program and discuss steps necessary to plan for and complete internal occupational health and safety management system (OHSMS) audits. Develop skills to document nonconformance findings, assess adequacy and effectiveness of corrective actions, and evaluate the adequacy, suitability and effectiveness of an internal audit program. Demonstrate a solid understanding of audit programs and processes and apply the knowledge to complete an OHSMS audit. Your registration includes a digital copy of ISO 45001-2018.
Instructor(s): Kenneth A. Clayman, SMS
- Use tools to develop an OHSMS internal auditing program
- Plan and complete internal OHSMS audits.
- Assess and improve your organization’s OHSMS based on ISO 45001
Measuring Safety Culture
Thursday, February 15 | Advanced | 0.7 CEUs
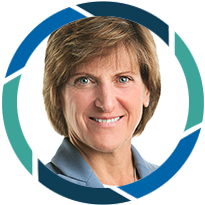
This advanced course actively engages the safety professional’s knowledge of management systems and safety culture to measure the heartbeat of their safety program. In this working session, attendees will simultaneously use qualitative and quantitative methods to assess and score the two main pillars of their safety program: safety management systems and operational culture. Participants will return to the workplace with a multi-dimensional look at their safety program. This course is ideal for advanced safety managers, safety committee members, and other safety and health stakeholders who have at least seven years of experience with management systems.
Instructor(s): Cynthia E Braun, CSP, CHMM, CIT
- Define ""safety culture"" and ""safety management system”
- Use an integrated measurement tool to assess and score key elements of your organization’s safety management system and safety culture
- Identify at least three ways to improve, support, and/or promote a positive safety culture and management system
Safety Management I
Monday, February 12 – Wednesday, February 14 | Beginner | 2.1 CEUs
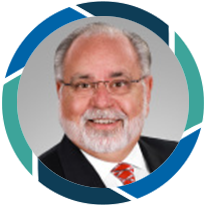
Occupational safety and health (OSH) processes have fundamental elements and conditions required by regulatory agencies. Develop a foundational understanding of these elements and examine techniques for creating an effective safety management system. Build on or confirm the current conditions of your OSH process to create a road map for an effective safety management system. This course is the first in a three-course series for obtaining ASSP’s Safety Management Certificate.
Instructor(s): James 'Skipper' Kendrick, Jr, CSP, FASSP
- Apply proven techniques to establish accountability for safety efforts
- Identify the elements of a safety management system and discuss strategies for implementing them
- Write effective policy statements and performance standards to help your management team execute its safety responsibilities
- Develop the ability to promote safety to various levels in the organization
- Describe the moral, financial, and legal responsibilities of today’s safety professional
- Create strategies to control workers’ compensation costs
- Establish a budget for a safety management effort
Safety Management II
Thursday, February 15 – Friday, February 16 | Beginner | 1.4 CEUs
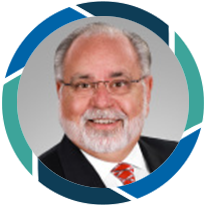
Build on what you learn in Safety Management I to take steps to implement a safety management system within your organization and practice techniques to measure its effectiveness. You will also gain insight and practical guidance on how to strengthen an existing safety management system. This course is the second in a three-course series for obtaining ASSP’s Safety Management Certificate.
Instructor(s): James 'Skipper' Kendrick, Jr, CSP, FASSP
- Review various types of safety management systems and evaluate their application to the safety function
- Practice methods for assessing the performance of a safety management system
- Evaluate leading metrics and determine how they may benefit your organization
- Use effective leadership and communication skills, training and ethical behavior to improve safety performance
Safety Through Accountability and Recognition: An Approach to Succeed at Management Commitment and Worker Engagement
Wednesday, February 21 | Intermediate | 0.4 CEUs
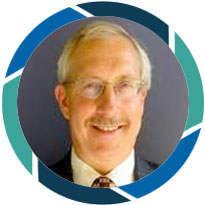
This course will use accountability metrics to provide a foundation for designing, implementing, and verifying management commitment. The balanced set of metrics and concepts from the new ANSI/ASSP Z16 standard will be part of the presentation. The benefits of worker participation at both the individual and team level will be presented, using similar metrics for recognition. Pitfalls of common recognition programs will also be presented.
Instructor(s): Paul A Esposito, CSP, CIH
- Define management accountability and commitment to occupational health and safety management systems
- Practice using a balanced set of process (logic) metrics to measure management accountability
- Develop recognition programs to motivate workforce participation without incident statistics
Safety Management Systems for Joint-Employer Environments
Tuesday, February 20 | Intermediate | 0.4 CEUs
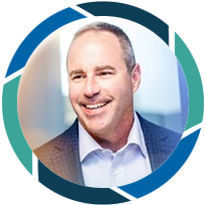
As the work landscape evolves, organizations are relying more on non-traditional employment arrangements, such as temporary and contract workers. To effectively manage the associated risks and pressures, businesses must transition from a traditional regulatory approach and implement robust occupational health and safety management systems (OHSMS). Gain practical and comprehensive guidance that will help you successfully integrate an OHSMS grounded in a recognized framework like ISO 45001 and ANSI/ASSP Z10. Gain the knowledge, strategies and skills you need to lead your organization through a continual improvement process, enabling strategic and tactical enhancements in joint-employer safety management. A copy of the textbook: Safety Management Systems in a Joint-Employer Environment, is included.
Instructor(s): Scott DeBow, CSP, ASP, ARM
- Develop a comprehensive understanding of the increasing business use and significance of joint-employer arrangements in today's work environment
- Recognize the limitations of a traditional compliance-based approach to workplace safety and health, while identifying the risk multipliers commonly associated with serious injuries and fatalities
- Summarize the knowledge and narratives required to effectively communicate change management and promote key elements of OHSMS across various shareholder functions
- Acquire practical tools and techniques to integrate a risk-based approach and use maturity modeling to achieve continuous improvement in a joint-employer environment
Technical Writing for the Safety Professional
Friday, February 16 | Intermediate | 0.7 CEUs

Enhance your credibility by mastering the art of safety writing. This course will cover content development, template creation and technical writing fundamentals to help you develop clear and accurate safety manuals, policies, programs, procedures and reports. Through interactive workshops, you will gain the skills to write concise, cohesive and technically correct documents that communicate important safety information.
Instructor(s): Cynthia E Braun, CSP, CHMM, CIT
- Differentiate between policies, programs, procedures and safety manuals, and develop content for each
- Evaluate the needs of your audience, use active voice and improve clarity
- Identify and eliminate words and phrases unsuitable for technical writing
- Review documents for accuracy, quality, grammar, spelling and punctuation
- Summarize basic document formatting elements