INTERMEDIATE LEVEL COURSES
BUSINESS AND LEADERSHIP SKILLS
ANSI/ASSP Z16: Safety Metrics For the Modern Safety Professional
Tuesday, February 13 | Intermediate | 0.7 CEUs
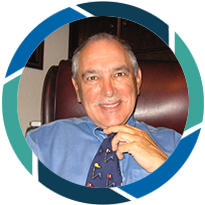
Modern safety professionals must understand many kinds of metrics and how to work with management to choose the right ones. Following the new ANSI/ASSP Z16.1 standard, this course will explore the use of balanced scorecards, leading indicators and other metrics that can help you understand your safety program’s effectiveness. Learn the history of traditional metrics, how they’ve been used and why they shouldn’t be the only way you measure success.
Instructor(s): C. Gary Lopez, MS, CSP, FASSP, DSS
- Apply traditional lagging indicators, such as incident rates and lost-time incident rates
- Select leading indicators and apply them to improve culture and management accountability for safety
- Explain the types of metrics being used to measure safety performance
- Measure losses beyond direct costs
- Understand the financial impact of key metrics
Communicating For Action: Is Anyone Even Listening?
Monday, February 12 | Intermediate | 0.7 CEUs
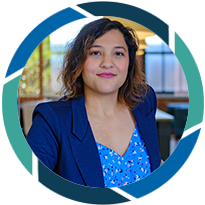
Refine your communication skills to inspire action and promote a culture where teams consider safety in all work. Join us and learn to understand your audience, deliver impactful messages and enhance your public speaking. Gain effective techniques for presenting technical information, getting project approval, building relationships, fostering trust and boosting your confidence, ultimately benefiting your organization.
Instructor(s): Camille P. Oakes, CSP, SMS, CIT
- Identify and explain three learning modalities: visual, aural and kinesthetic
- Develop a safety communications plan for your organization using a template
- Identify safety drivers and tailor a safety message based on motivation
- Assess your own communication skills and gaps
Ethics for OSH Professionals
Wednesday, February 21 | Intermediate | 0.5 CEUs
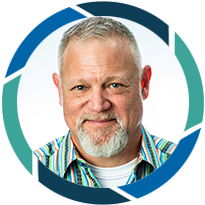
Today’s OSH professionals can encounter a wide range of ethical dilemmas. Build your knowledge of how you can use professional codes of ethics to identify, analyze, navigate and resolve these dilemmas. By using facts and promoting ethical practices, you can minimize harm, foster a positive company culture and support your organization’s long-term success and profitability. Explore the drivers influencing ethical decision-making and the theoretical framework supporting the use of such drivers. This course has been designed to meet the ethics training requirement established for certified industrial hygienists by the Board of Global EHS Credentialing (BGC), an organization that replaced American Board of Industrial Hygiene. Visit the BGC website to learn more. This course also meets the ethics requirement established for recertification by the Board of Certified Safety Professionals. Visit the BCSP website to learn more.
Instructor(s): Daniel J Snyder, Ph.D., CSP, CHST, OHST, CIT
- Review professional codes of conduct for OSH professionals
- Build a better understanding of how the various codes of ethics apply to your practice as an OSH professional
- Explore various approaches for resolving ethical issues
- Practice applying various ethical principles through real-life scenarios to resolve ethical issues
- Identify and analyze steps you can take to avoid future ethical dilemmas
How to Write and Tell Effective and Powerful Stories
Monday, February 19 | Intermediate | 0.7 CEUs
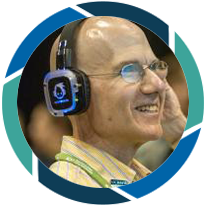
Stories are one of the most powerful tools we have, helping us bond, relate, empathize, contextualize, persuade, communicate and even survive. In this course, you'll write, share, listen, give and get feedback, and get comfortable with the storytelling process. By the end, you'll have written a couple of scenes, a story spine, an opener and an ending using a worksheet that will guide you toward an effective structure.
Instructor(s): Jonathan T Klane, M.S., CSP, CIH, CHMM, CIT
- Create narrative-based content to use in future training courses
- Compare and contrast the benefits (and challenges) of using narrative rather than traditional approaches
- Explain the typical structure and format of creative nonfiction
- Demonstrate how to create meaningful stories for communication, persuasion or training courses
- Communicate and train more effectively with storytelling
Improve Your Pre-Task Planning in 30 Days or Less!
Thursday, February 22 | Intermediate | 0.4 CEUs
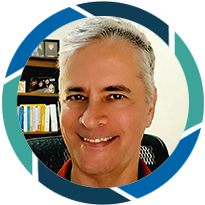
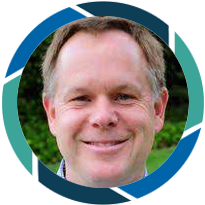
Are your pre-task plans, job hazard analyses or toolbox talks truly effective, or have they become a superficial exercise that doesn’t improve safety and health? Practice and master a systematic approach that will transform your pre-task planning processes into valuable tools that help you assess your organization’s leadership and culture. Effectively using these metrics will enable you to cultivate front-line leaders who can empower their project teams to anticipate safety hazards, foster trust, nurture respect and create a culture of safety ownership.
Instructor(s): Chuck Pettinger and Barry Nelson
- Evaluate the effectiveness of conversations (as opposed to checklists) in gauging the health of your organization’s front-line leadership and culture
- Apply five proven techniques to transform your pre-task planning processes into engaging activities that encourage project teams to communicate, recognize safety risks and safeguard each other
- Use leadership metrics to develop influential front-line leaders, assess performance and enhance your organization’s safety culture
Learn How to Persuade Based on Science and Research
Wednesday, February 21 | Intermediate | 0.7 CEUs

Master the art of persuasion in this course that draws on centuries of scientific research. Through interactive exercises and practical applications, you'll strengthen your ability to persuade while learning from the experiences of other safety and health professionals. Overcome skepticism and doubt by harnessing the power of persuasion and become a more influential communicator.
Instructor(s): Jonathan T Klane, M.S., CSP, CIH, CHMM, CIT
- Demonstrate persuasion techniques
- Describe how certain persuasive strategies work
- Explain why many attempts at persuasion fail
Make Your Safety Training Stick: Improve Retention and Get Better Results
Thursday, February 15 – Friday, February 16 | Intermediate | 1.4 CEUs

Go beyond the basics to improve your safety training. This course will focus on gaining the attention of trainees and management, designing methods for increased retention, and implementing techniques to help trainees apply their knowledge. Learn how to create your own activities, backed by science, that help keep people safe. A copy of the textbook: Make Your Safety Training Stick: Improve Retention and Get Better Results, is included.
Instructor(s): Linda M Tapp, CSP, ALCM
- Understand the challenges associated with retention and transfer and ways to overcome these challenges
- Understand accelerated learning principles and research-based learning science
- Create and deliver safety training that provides greater opportunities for retention and transfer
- Facilitate interactive learning activities that have a beneficial impact on the success of training classes
Making Safety Stick
Tuesday, February 20 | Intermediate | 0.7 CEUs

Explore communication principles and discover the secrets behind impactful safety training. This session will offer a fresh perspective on delivering safety messages, ensuring comprehension, improving retention and driving meaningful change. Learn innovative techniques that will not only help your audience understand the information but leverage it long term.
Instructor(s): Eldeen E Pozniak, CMIOSH, CRSP
- Analyze the factors that contribute to the widespread adoption of concepts and new behaviors
- Explore how communication strategies improve retention
- Apply emotional appeal and storytelling techniques to reinforce the effectiveness of messages
Measuring Safety Cultural Maturity
Tuesday, February 20 | Intermediate | 0.4 CEUs
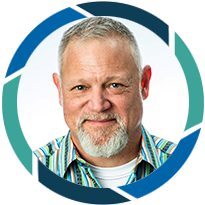
This course presents a cutting-edge, mixed-method, experimental research design model for assessing safety culture maturity in global organizations. Participants will explore the application of qualitative and quantitative instruments to identify key indicators of safety culture maturity and analyze the outcomes. The researcher will share insights and findings from the study, offering a comprehensive summary of the assessment process and its implications.
Instructor(s): Daniel J Snyder, Ph.D., CSP, CHST, OHST, CIT
- Define safety culture
- Discuss mixed methods for safety culture spectral analysis
- Describe the determining factors of safety culture maturity
Qualified Safety Trainer Workshop
Friday, February 23 | Intermediate | 0.4 CEUs
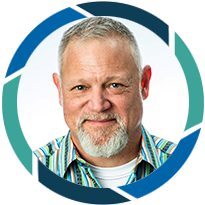
In this interactive train-the-trainer workshop, you will develop essential skills that improve the ways you teach others about workplace safety and health. Explore the core competencies of a safety trainer, including instructional techniques, communication strategies and engaging delivery methods. Gain practical tips for designing and presenting safety training sessions that promote knowledge retention and behavioral change.
Instructor(s): Daniel J Snyder, Ph.D., CSP, CHST, OHST, CIT
- Discuss the ANSI/ASSP Z490.1 criteria for accepted practices in occupational safety and health training
- Describe the ADDIE model for instructional systems design
- Explain best practices and instructional strategies for adult learners
Safety Leadership and Emotional Intelligence: How Smart Are You?
Tuesday, February 13 | Intermediate | 0.7 CEUs

Occupational safety and health leaders often have strong technical skills, focusing on hazards, risks and controls. But without strong soft skills, even their best safety initiatives may fail to gain leadership approval and influence outcomes. Learn the importance of emotional Intelligence in navigating challenges, working with stakeholders and cultivating your organization’s safety culture.
Instructor(s): Eldeen E Pozniak, CMIOSH, CRSP
- Apply emotional intelligence concepts
- Apply leadership and management skills, recognizing when to use each approach based on the circumstances
- Evaluate the importance of emotional intelligence in occupational safety and health leadership
Smooth Operator: Soft Skills for Safety Professionals
Wednesday, February 14 | Intermediate | 0.7 CEUs
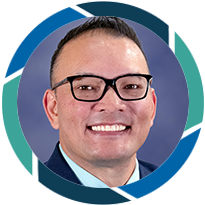
Unleash the power of soft skills to increase safety compliance and captivate your workforce. This immersive full-day session delves deep into transformative interpersonal techniques that win the hearts and minds of workers, resulting in significant safety improvements. Learn to leverage consistency, positivity, empathy and storytelling to cultivate a robust safety culture and inspire faith in your program, whether you're a safety professional or a front-line supervisor seeking enhanced engagement.
Instructor(s): Tim Page-Bottorff, M.S., CSP, CIT
- Demonstrate the value of soft skills
- Analyze what soft skills can and cannot do
- Examine research on relationship building and recognize its importance in safety
- Identify the seven soft skills that will make your safety program more efficient
- Apply the seven soft skills through interactive practice with other safety professionals
Strategies For Safety Excellence: Advancing Safety in Your Organization and Career
Friday, February 16 | Intermediate | 0.7 CEUs
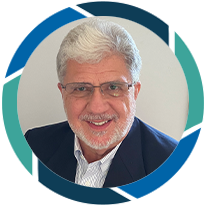
There are many challenges that keep organizations from achieving safety excellence. This course will explore how to create an effective safety strategy that emphasizes learning and working with leaders to anticipate and address risks. It will use an in-depth case study of CEO Paul O’Neill’s tenure at Alcoa to illustrate how safety can become an organizational value.
Instructor(s): Earl Blair, Ph.D., CSP, FASSP
- Understand past failures and successes to promote safety
- Describe how strategy must be deliberate to sustain safety excellence
- Use foresight to influence safety outcomes
The Safety Superpower: Influence!
Monday, February 12 | Intermediate | 0.7 CEUs
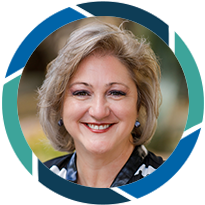
As safety professionals, we need to lead, persuade others and maximize our personal impact on individuals, groups and organizations. The ability to influence is an essential leadership skill. To influence is to have an impact on the focus, attitudes, opinions, choices and behaviors of others.
Instructor(s): Eldeen E Pozniak, CMIOSH, CRSP
- Understand influential leadership concepts
- Describe and apply the six fundamental principles of persuasion
- Use logical, emotional and cooperative appeals to better protect your team
We Can Fight Bias
Friday, February 23 | Intermediate | 0.7 CEUs
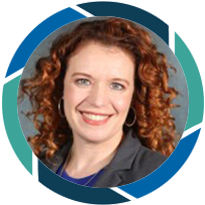
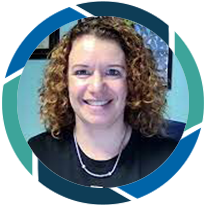
Bias is an inclination in favor of or against an idea or thing and is often prejudicial. In science and engineering, bias is a systematic error. People may develop biases that impact others’ professional development, safety and health. Why do we have biases? Where do they come from? And how do we shed them?
Instructor(s): Christina R Roll, M.S., CSP, CIH and Joy Jacobsen
- Discuss, describe and define bias and its role in personal and professional development
- Anticipate bias in the workplace
- Recognize where bias can be a strength
- Evaluate the impact of bias in the workplace
- Control one's biases and learn to move through them
CERTIFICATE PREPARATION
Certified Safety Professional (CSP) Exam Preparation
Wednesday, February 14 – Friday, February 16 | Intermediate | 2.1 CEUs

Learn what you need to know to pass the Certified Safety Professional (CSP) certification exam. Complete practice questions and review answers that align with the Board of Certified Safety Professionals (BCSP) blueprint for the CSP exam. Get answers to your questions about the testing process and get practical guidance on what you should do to prepare. You need a TI-30XS scientific calculator to participate in this course.
Instructor(s): Patrick Karol, CSP, SMS, CIT
- Describe the CSP exam blueprint
- Describe the Pearson VUE testing process
- Describe the certification requirements and scoring
- Review test-taking and study strategies
- Demonstrate an understanding of the CSP exam blueprint by answering sample questions
- Evaluate knowledge gaps and strengths
- Develop a study plan
- Locate resources to fill knowledge gaps and reinforce strengths
Construction Health and Safety Technician (CHST) Exam Preparation
Wednesday, February 14 – Friday, February 16 | Intermediate | 2.1 CEUs
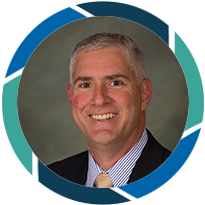
Learn what you need to know to pass the Construction Health and Safety Technician (CHST) certification exam. Participate in a comprehensive review of the exam blueprint, complete sample questions and receive additional quizzes to take home for extra practice. You need a TI-30XS scientific calculator to participate in this course.
Instructor(s): Robert Hites, CSP, CHST, CIT, SMS
- Describe the CHST exam blueprint
- Describe the Pearson VUE testing process
- Describe certification requirements and scoring
- Review test-taking and study strategies
- Demonstrate an understanding of the CHST exam blueprint by answering sample questions
- Evaluate knowledge gaps and strengths
- Develop a study plan
- Locate resources to fill knowledge gaps and reinforce strengths
RISK ASSESSMENT AND MANAGEMENT
Applied Ergonomics Risk Assessment
Wednesday, February 14 | Intermediate | 0.7 CEUs
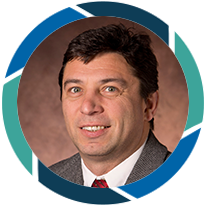
This applied ergonomics risk assessment course gives participants a foundational understanding of an ergonomics program. Participants will receive a set of essential ergonomics risk assessment tools. The participants will learn to use tools for ergonomics hazard identification, analyze and evaluate ergonomic risks, and apply risk reduction concepts.
Instructor(s): Georgi Popov, Ph.D., CSP, ARM, SMS, QEP
- Describe ergonomics hazards
- Use appropriate ergonomics risk assessment terminology
- Differentiate between fundamental ergonomics hazard identification tools and semiquantitative ergonomics risk assessment tools
- Evaluate various ergonomics risk assessment methodologies
- Develop a business case for ergonomics interventions
Confined Space Assessment, Entry and Rescue
Monday, February 12 | Intermediate | 0.7 CEUs
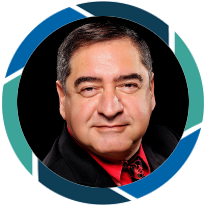
Master the knowledge and skills to safely assess, enter and perform confined space rescues in this course. Gain insights into air monitoring, ventilation, training requirements, developing a written program, implementing permits, managing contractors and executing effective retrieval methods. Engage in practical learning experiences with a confined space simulator and explore the latest equipment during hands-on demonstrations, ensuring you are well-prepared to handle confined space operations.
Instructor(s): Jay Jamali, CSP, CHMM, CHCM
- Assess a site to determine if it qualifies as a permit-required confined space
- Employ safe entry protocols for permit-required confined spaces
- Use safe rescue procedures to extract workers from permit-required confined spaces
- Develop a site-specific confined space entry and rescue program
Creating, Implementing and Sustaining Respiratory Protection Programs in Healthcare
Monday, February 19 | Intermediate | 0.7 CEUs
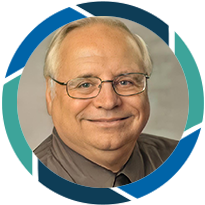
Expand your knowledge and build the skills you need to establish and maintain comprehensive respiratory protection programs in a healthcare setting. It is critical to protect all workers, including those in facility services, from respiratory hazards such as airborne pathogens, occupational exposures, surgical smoke and antineoplastic drugs. Course topics include source capture and control, total body exposure, hazard-specific respiratory protection, and important standards and certifications that address these gaps — including requirements from OSHA, The Joint Commission, Centers for Disease Control and Prevention/National Institute for Occupational Safety and Health, and the National Personal Protective Technology Laboratory. You will also gain new insight on HAZWOPER requirements for the hospital emergency response team, with a focus on first receivers. By implementing best practices and aligning with key standards, you will be better equipped to ensure the safety and well-being of healthcare workers and create a culture of protection and care.
Instructor(s): Dennis A Terpin, Ph.D., OHST
- Identify key administrative components of a healthcare respiratory protection program in accordance with 29 CFR 1910.134(c)
- Review the interplay and alignment of requirements between The Joint Commission, CDC, NIOSH and OSHA
- Apply an all-hazards approach to develop a risk-based healthcare respiratory protection program that addresses various occupational risks in a healthcare setting
- Recognize the limitations of respirators used in healthcare workplaces to support informed decision-making and appropriate selection of respiratory protective equipment
Electrical Safety II: Electrical Safe Work Practices with Application of NFPA 70E (2024 Edition)
Wednesday, February 14 – Thursday, February 15 | Intermediate | 1.4 CEUs
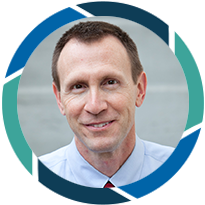
Participate in an in-depth, comprehensive review of electrical safe work practices, procedures, risk assessment and risk-reduction techniques outlined in the revised 2024 edition of NFPA 70E. Develop knowledge to interpret code requirements as they apply to energized electrical work situations.
Instructor(s): Paul A. Zoubek, CSP, CIH
- Identify NFPA 70E as a best practice standard
- Evaluate worker protection measures in accordance with the hierarchy of controls
- Use safety-related work practices for energized systems
- Implement risk assessment procedures outlined in the 2024 edition of NFPA 70E
Machine Safety Risk Assessment and Job Hazard Analysis
Monday, February 12 | Intermediate | 0.7 CEUs
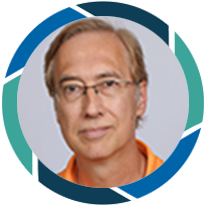
Learn to use the task-based risk assessment methodology specified in Robotics Industry Association standard TR R15.306-2016. This course will empower you to conduct any machine safety assessment, going beyond robotic systems. Master the job hazard analysis process to identify and mitigate risks, improving safety performance.
Instructor(s): Gary J Garrahan, CHMM
- Identify machine safety hazards and recognize potential risks
- Analyze the concept of risk and apply clear criteria to determine both initial risk levels (prior to considering safety features) and residual risk
- Evaluate the design and integration requirements for safety-related parts of control systems, ensuring the selection of appropriate risk-reduction measures
- Prioritize risk-reduction measures when faced with existing machines and multiple hazards
- Perform a job hazard analysis using a methodology aligned with machine safety risk assessments
Managing Risk, Not Safety
Monday, February 12 | Intermediate | 0.7 CEUs

Transition seamlessly from a hazard-based safety program to a risk-based approach with this comprehensive course. Discuss the evolution of risk management and delve into concepts such as acceptable risk and residual risk that play a pivotal role. Gain valuable insights into the effective utilization of risk management strategies and processes, equipping you to navigate challenges
Instructor(s): C. Gary Lopez, M.S., CSP, FASSP
- Analyze the changing role of the modern safety professional
- Apply risk management techniques in the context of occupational safety
- Assess the impact of safety professionals’ expanded responsibilities
- Differentiate between regulations and risks, understanding their distinct roles in shaping safety practices
- Examine the relationship between a safety management system, the application of controls and safety culture
NFPA 70E Policies, Procedures and Programs for Electrical and Mechanical Contractors
Wednesday, February 21 | Intermediate | 0.4 CEUs
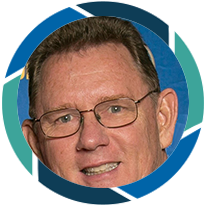
Enhance your understanding and proficiency in implementing the policies, procedures and programs required to safely conduct electrical work in various settings. Review key aspects of NFPA 70E and discuss relevant OSHA regulations and consensus standards to help you navigate the complex landscape of electrical safety and better protect team members who perform electrical work.
Instructor(s): Wesley Lamar Wheeler, SMS
- Explain how adhering to the requirements outlined in NFPA 70E will enable your team to perform electrical work safely and mitigate related risks
- Identify the specific policies and programs needed to comply with both OSHA regulations and the NFPA 70E consensus standard, including the responsibilities of employers, employees and owners
- Determine the appropriate training and qualification requirements for workers engaged in electrical testing, commissioning and troubleshooting activities to ensure their competencies
- List and apply the required steps involved in establishing an electrical safe work condition, including the implementation of absence of voltage testing procedures to verify the absence of electrical energy
- Understand and perform effective shock and arc-flash risk assessments, employing industry best practices to assess and mitigate potential hazards associated with electrical work
Prevention Through Design
Thursday, February 15 – Friday, February 16 | Intermediate | 3.0 CEUs
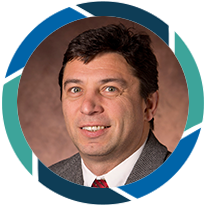
Gain practical guidance on how to apply prevention through design (PTD), a core methodology for reducing risk. As defined in ANSI/ASSP Z590.3-2021, a widely used voluntary national consensus standard, PTD provides a framework and process for implementing risk assessment concepts in the various phases of a system’s life span — from initial concept and design to use and then decommission. Review the various risk assessment tools and methods identified in the standard and discuss the PTD hierarchy of risk treatment. Practice applying PTD methods and concepts to real-world incidents as you work through modules that include short videos, scenarios, interactive tools, and assignments. Your registration includes a copy of ANSI/ASSP Z590.3-2021 Prevention through Design Guidelines for Addressing Occupational Hazards and Risks in Design and Redesign Processes. This course is the second in a three-course series for obtaining ASSP’s Risk Management Certificate.
Instructor(s): Georgi Popov, Ph.D., CSP, ARM, SMS, QEP
- Review the role of prevention through design in the risk assessment/ management process
- Develop deeper understanding of various tools for PTD interventions and product design
- Assess the PTD hierarchy of risk treatment
- Practice applying PTD methods and concepts to real-world examples
- Discuss effective ways to align safety and health interventions with business goals and objectives
- Develop a PTD implementation plan
Risk-Based Incident Investigation
Tuesday, February 20 | Intermediate | 0.4 CEUs
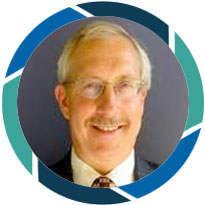
Develop essential skills and techniques to effectively analyze incidents, uncover root causes and prioritize risk mitigation measures. By integrating risk-centric thinking with causal factor analysis and the five whys method, you will gain practical experience via scenario-based exercises designed to help you identify successes and failures in hazard identification and control. Following the proven eight disciplines (8D) approach, you will navigate through eight comprehensive steps, culminating in the identification of root causes and the implementation of effective management systems. Other topics include the significance of categorizing and trending loss data by hazardous energies and control failures, and effective ways to distinguish between fatal or serious incidents and significant incident frequencies.
Instructor(s): Paul A Esposito, CSP, CIH
- Identify the most impactful risk-based data to determine causal factors and root causes
- Implement a systematic methodology to determine immediate, corrective and preventive actions following incident investigations
- Effectively trend incident data over time to identify patterns, weaknesses in management systems and opportunities for improvement
- Quantify incident data inputs and outputs to establish strategic leading metrics
- Qualify incident data to accurately classify work incidents and enable appropriate resource allocation
SAFETY MANAGEMENT SYSTEMS
Conforming With ANSI/ASSP Z16.1: Creating a Balanced Set of Metrics
Monday, February 19 | Intermediate | 0.4 CEUs
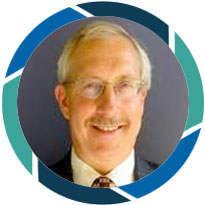
Discuss effective strategies and skills to implement a balanced set of metrics to evaluate your organization's occupational safety and health performance. Through a focus on the leading, lagging and value-based metrics outlined in the ANSI/ASSP Z16.1 standard, you will deepen your understanding of how these metrics can help you drive organizational improvement, elevate risk management and enhance your organization’s overall performance. A copy of the ANSI/ASSP Z16.1-2022 Safety and Health Metrics and Performance Measures is included.
Instructor(s): Paul A Esposito, CSP, CIH
- Apply the principles and concepts of a balanced set of leading, lagging and value-based metrics
- Interpret and analyze value-based metrics that impact an organization's financial results to identify opportunities for improvement
- Demonstrate how your organization can use multiple leading metrics to predict and influence lagging metrics
- Communicate the relationship between a balanced set of metrics and effective risk reduction
- Align safety metrics with organizational goals and performance objectives
Corporate Safety Management
Monday, February 12 – Wednesday, February 14 | Intermediate | 2.1 CEUs
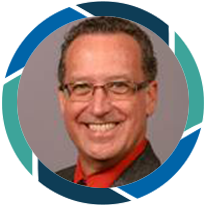
Learn new ways to tackle challenges, craft solutions and apply the skills needed to successfully position safety in your organization. Explore corporate management systems and organizational cultures and develop insight on how you can influence them from a safety perspective. You will review corporate reporting relationships, occupational safety and health (OSH) staffing and the tenets of OSH management systems. You will also use tools to assess your organization’s current safety process and identify ways to adjust it to achieve desired state. Develop your ability to apply negotiation and leadership skills to influence decision-making that affects corporate structure. Take away a new understanding of how to apply corporate safety management concepts and systems and how to lead and influence positive outcomes that change your workplace. This course is the third in a three-course series for obtaining ASSP’s Safety Management Certificate.
Your registration includes a copy of ISO 45001-2018.
Instructor(s): James Boretti, CSP
- Develop a safety management system to support your organization’s strategic and business goals
- Effectively assess and measure your organization’s safety performance
- Discuss the influence of corporate culture and develop skills to effect changes that help your organization embrace OSH efforts
- Justify where the safety function is best positioned within your organization’s corporate structure
- Apply leadership, negotiation and communication skills to positively influence corporate safety management system
- Analyze key initiatives for creating high-impact safety performance
- Define and discuss best practices for safety performance enhancement
- Analyze appropriate adjustments to the safety effort in response to corporate mergers, downsizing, rightsizing and reorganizing
Implementing ISO 45001
Monday, February 19 – Wednesday, February 21 | Intermediate | 2.1 CEUs

Through a blended learning approach, develop the knowledge and confidence to successfully implement an occupational health and safety management system (OHSMS) as an integral part of your organization’s overall business operations and objectives. Organizations that adopt the standard as part of their business practices, goals and objectives can better protect their workers, brand reputation, supply chain and future growth on a global level. Your registration includes a digital copy of ISO 45001-2018.
Instructor(s): Victor M. Toy, CSP, CIH
- Create a compelling story around developing and implementing an ISO-45001-compliant OHSMS
- Explain the importance and value of implementing an OHSMS following the ISO 45001 standard
- Define key terminology and guidelines related to the implementation of the ISO 45001 standard
- Navigate the ISO 45001 standard and its main sections
- Assess performance of your OHSMS, leveraging the success factors listed in the standard to continuously improve the process
- Translate knowledge gained into an actionable plan for initiating your own OHSMS development and implementation
Internal OHSMS Auditing Using ISO 45001
Thursday, February 22 – Friday, February 23 | Intermediate | 1.4 CEUs
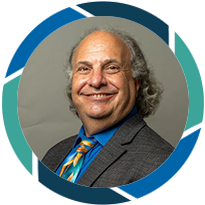
Examine ISO 45001-2018 from an auditor's perspective. Review components of an effective internal audit program and discuss steps necessary to plan for and complete internal occupational health and safety management system (OHSMS) audits. Develop skills to document nonconformance findings, assess adequacy and effectiveness of corrective actions, and evaluate the adequacy, suitability and effectiveness of an internal audit program. Demonstrate a solid understanding of audit programs and processes and apply the knowledge to complete an OHSMS audit. Your registration includes a digital copy of ISO 45001-2018.
Instructor(s): Kenneth A. Clayman, SMS
- Use tools to develop an OHSMS internal auditing program
- Plan and complete internal OHSMS audits.
- Assess and improve your organization’s OHSMS based on ISO 45001
Safety Through Accountability and Recognition: An Approach to Succeed at Management Commitment and Worker Engagement
Wednesday, February 21 | Intermediate | 0.4 CEUs
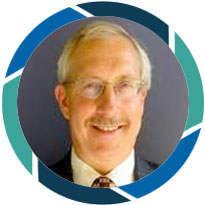
This course will use accountability metrics to provide a foundation for designing, implementing, and verifying management commitment. The balanced set of metrics and concepts from the new ANSI/ASSP Z16 standard will be part of the presentation. The benefits of worker participation at both the individual and team level will be presented, using similar metrics for recognition. Pitfalls of common recognition programs will also be presented.
Instructor(s): Paul A Esposito, CSP, CIH
- Define management accountability and commitment to occupational health and safety management systems
- Practice using a balanced set of process (logic) metrics to measure management accountability
- Develop recognition programs to motivate workforce participation without incident statistics
Safety Management Systems for Joint-Employer Environments
Tuesday, February 20 | Intermediate | 0.4 CEUs
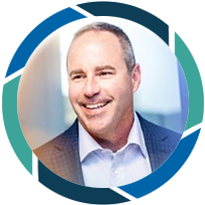
As the work landscape evolves, organizations are relying more on non-traditional employment arrangements, such as temporary and contract workers. To effectively manage the associated risks and pressures, businesses must transition from a traditional regulatory approach and implement robust occupational health and safety management systems (OHSMS). Gain practical and comprehensive guidance that will help you successfully integrate an OHSMS grounded in a recognized framework like ISO 45001 and ANSI/ASSP Z10. Gain the knowledge, strategies and skills you need to lead your organization through a continual improvement process, enabling strategic and tactical enhancements in joint-employer safety management. A copy of the textbook: Safety Management Systems in a Joint-Employer Environment, is included.
Instructor(s): Scott DeBow, CSP, ASP, ARM
- Develop a comprehensive understanding of the increasing business use and significance of joint-employer arrangements in today's work environment
- Recognize the limitations of a traditional compliance-based approach to workplace safety and health, while identifying the risk multipliers commonly associated with serious injuries and fatalities
- Summarize the knowledge and narratives required to effectively communicate change management and promote key elements of OHSMS across various shareholder functions
- Acquire practical tools and techniques to integrate a risk-based approach and use maturity modeling to achieve continuous improvement in a joint-employer environment
Technical Writing for the Safety Professional
Friday, February 16 | Intermediate | 0.7 CEUs

Enhance your credibility by mastering the art of safety writing. This course will cover content development, template creation and technical writing fundamentals to help you develop clear and accurate safety manuals, policies, programs, procedures and reports. Through interactive workshops, you will gain the skills to write concise, cohesive and technically correct documents that communicate important safety information.
Instructor(s): Cynthia E Braun, CSP, CHMM, CIT
- Differentiate between policies, programs, procedures and safety manuals, and develop content for each
- Evaluate the needs of your audience, use active voice and improve clarity
- Identify and eliminate words and phrases unsuitable for technical writing
- Review documents for accuracy, quality, grammar, spelling and punctuation
- Summarize basic document formatting elements